Two years after Silver Fern Farms’ Te Aroha beef processing operation was destroyed by fire in December 2010, a state of the art facility opened in December and is up and running in its place.
Silver Fern Farms’ new $67m Te Aroha plant is a hot-boned beef processing operation designed for best practice processing of manufacturing cows, bulls, steers and heifers from farmer suppliers across the Waikato region.
It joins a network of 23 Silver Fern Farms processing facilities employing over 7,000 staff throughout the country. Te Aroha will employ up to 380 staff when operating at full capacity with two shifts in peak season with an annual capacity of 125,000 cattle.
At the plant’s official opening in December last year, Silver Fern Farms chief executive, Keith Cooper, said the new design reflected the company’s focus on plant economics and best practice processing and the investment was testament to the co-operative’s strong confidence in the sector.
The plant has been designed in consultation with internationally recognised experts in process layout and ergonomics. It is compliant with New Zealand, EU, US Department of Agriculture (USDA), and Chinese hygiene requirements and also to halal standards for the Middle East, Malaysia and Indonesia.
Te Aroha incorporates the latest meat processing technologies; including sophisticated traceability and yield measurement systems.
The plant is configured with a custom-designed two-level Milmeq slaughterboard. Extensive use is made of RFID tags, with scanning stations at slaughter, grading and boning stages, monitored through the new Marel Streamline computerised deboning and trimming system. The process has been designed for complete traceability and to enable Silver Fern Farms to closely monitor key production indicators.
Rapid feedback
This system has the capability to deliver rapid feedback to plant staff on how closely they are meeting customer requirements for particular cuts. This fits with Silver Fern Farms’ plate-to-pasture strategy where consumer requirements are driving process improvements in order for the company to extract higher value returns from products.
This data collection is underpinned by the Primary Growth Partnership FarmIQ joint venture programme – an investment of $151 million by Silver Fern Farms, Landcorp Farming, Tru-Test Group and the Ministry of Primary Industries.
Over the seven years of the programme the aim is to integrate the red meat value chain to maximise returns to farmer partners.
For farmers, information collected at the Te Aroha plant on meat yield and quality can be used to inform farm management decisions as they look for avenues to lift farm system performance. This information can also be married with information from the insights FarmIQ will bring from consumers so farmers can produce to target higher-value returns from specific consumers.
Trimming to specification
Following break-down and deboning, the primal cuts are distributed to work stations on the trimming line, based on operator availability. They are then trimmed according to individual specifications and all cuts are fully traceable. The automated conveyor system will enable Silver Fern Farms to closely monitor and control critical key production indicators in real time throughout the complete processing cycle. These include yield, throughput, cutting performance, giveaway and loss of sales. These are automatically registered and monitored for the entire line as well as for the individual operator, using Innova intelligent production control software.
Provision has been made for future installation of technologies including robotic bagging.
Sustainability top-of-mind
Eco-efficiency and sustainability were top-of-mind considerations. As a result, the new plant uses significantly less electricity and water per head and discharges less effluent per animal processed, setting new benchmarks in line with global customer requirements.
Keith Cooper says the rebuild gives the company an opportunity to review the environmental footprint of the operation. “Our focus is improving environmental efficiency while reducing costs through better use of resources and reduction of waste.”
The plant has also been orientated to ensure noisy areas and truck movements are at the centre or the rear of the plant, away from neighbours. Every effort has been made to reduce noise coming from the plant, even to the point that refrigeration equipment, undamaged by the fire, was relocated.
Health and safety focus
Health and safety was another major focus for the company when developing the specifications for the new facility. Process areas have been designed to minimise workstation hazards. A suite of solutions to minimise lifting, turning and carrying were factored into the design. The boning room has European-designed workstations intended to maximize productivity by minimising operator fatigue and discomfort. At trim stations adjustable work heights, reach to meat and easy access to work positions make for a safer and more comfortable work environment for staff.
Separate viewing areas let people observe the slaughter and boning processes without interfering with workers on the floor. The plant layout also factors in separation between pedestrian and heavy vehicle movement areas to provide a safer environment for people.
Throughout the rebuilding process, Silver Fern Farms endeavoured to provide alternative options for staff whose livelihoods were affected by the fire, to the extent of making positions available at other company plants in the North Island and providing accommodation supplements in the early stages. The company’s significant capital spend also has provided positive spin-offs to the local economy as a result of the number of contractors throughout the region engaged during the course of construction.
Cooper says the co-operative’s loyal farmer-suppliers in the area were particularly supportive of the company through the re-build.
“We are grateful to those suppliers who have stood by us and persevered while we got the new plant up and running – we know the disruption has been an inconvenience for many. But we are enthusiastic about the service levels and advantages we can now offer them as a result of our investment.”
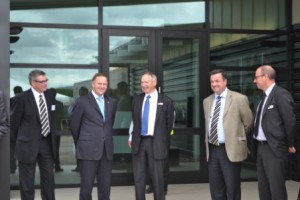
Pictured at the Te Aroha opening are (left to right): local MP Scott Simpson; John Key; Eoin Garden chairman Silver Fern Farms; Keith Cooper, chief executive Silver Fern Farms; Kevin Winders, chief operating officer Silver Fern Farms.
This article has appeared in Food NZ magazine (February/March 2013) and is reproduced here with permission.